Le Lean Manufacturing est aujourd’hui une référence incontournable en matière d’optimisation des processus industriels et de recherche de l’excellence opérationnelle. Derrière ce concept se cache la contribution d’un ingénieur japonais visionnaire : Taiichi Ohno. Ce père du Système de Production Toyota a bouleversé les approches traditionnelles en réinventant l’organisation du travail sur les chaînes de montage automobiles après la Seconde Guerre mondiale.
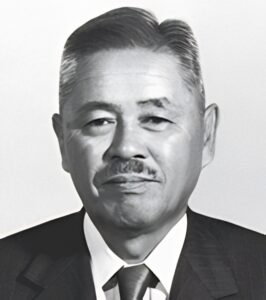
Né en 1912, Taiichi Ohno a rejoint Toyota en tant qu’ouvrier spécialisé à l’âge de 19 ans en 1932, après avoir terminé ses études secondaires.
Grimpant les échelons, il occupera différents postes avant d’être nommé en 1943 responsable des stocks, puis directeur de l’atelier usinant les blocs moteurs. C’est là qu’il commencera à réfléchir et expérimenter à de nouveaux principes de production. L’inspiration viendra d’un voyage aux Etats-Unis en 1950. Impressionné par les performance de Ford, il comprend cependant que le modèle du Fordisme n’est pas transposable au Japon.
En effet, après la Seconde Guerre mondiale, Toyota fait face à la pénurie de ressources et de capitaux. L’entreprise ne peut se permettre les stocks importants. Son marché est trop restreint pour permettre une production de masse à l’américaine. Taiichi Ohno y voit une opportunité de repenser totalement le fonctionnement des usines. Il introduit deux principes directeurs : « juste-à-temps » (produire uniquement les quantités nécessaires au fur et à mesure) et « jidoka » (autonomation, ou qualité intégrée avec autocontrôle).
La demande jouera désormais un rôle crucial dans la détermination du nombre et du type de véhicules. Plus aucune fabrication ne pourra être lancée sans une commande préalable. De plus, il sera strictement interdit de stocker des pièces sur le sol. L’approvisionnement de chaque poste de travail est limité à ce qui peut être contenu dans un chariot, correspondant à la quantité nécessaire pour assembler cinq véhicules.
Le Toyota Production System était né.
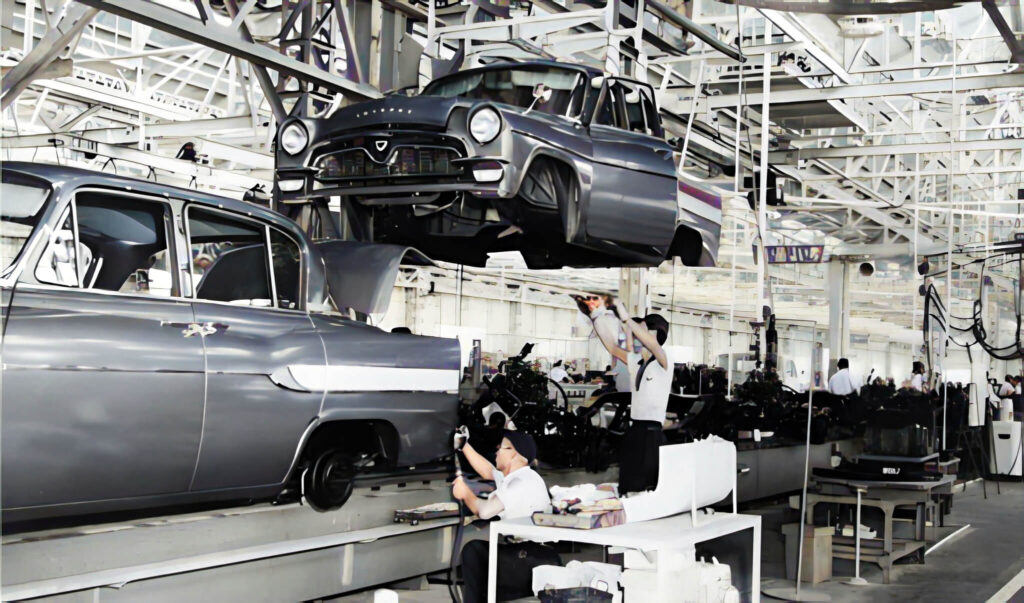
Pour concrétiser sa vision, Ohno a mis au point toute une panoplie d’outils et méthodes visant à lisser la production, optimiser les flux et impliquer le personnel :
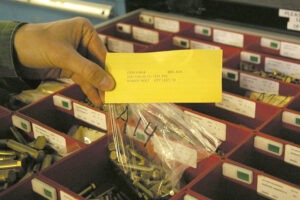
- Le kanban (étiquettes) pour tirer visuellement la production en fonction des besoins aval.
- L’heijunka (lissage de la production) pour produire de petits lots fréquents.
- La « chasse aux muda » (7 gaspillages) pour éliminer tout ce qui n’ajoute pas de valeur.
- Le management visuel avec des indicateurs clairs et parlants.
- Le kaizen et l’amélioration continue impliquant tous les niveaux hiérarchiques.
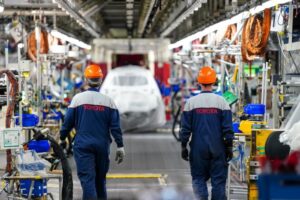
Le déploiement du TPS à grande échelle dans les usines Toyota a cependant été semé d’embûches. Aux réticences initiales des opérateurs s’ajoutaient des doutes de la direction sur la viabilité du nouveau système. Mais grâce à la ténacité d’Ohno et de son équipe, les premières lignes pilotes ont pu démontrer des gains spectaculaires de productivité et de réduction des défauts. La formation massive des salariés a alors permis une propagation du TPS dans toutes les usines de la marque.
Le succès du modèle Toyota n’est pas passé inaperçu et les principes du Lean se sont peu à peu répandus dans de multiples secteurs industriels et de services.
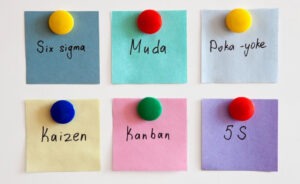
Des entreprises comme Dell, Nike ou encore des hôpitaux américains ont adopté ces méthodes d’élimination des gaspillages, de flux tendus et d’implication du personnel. Le mouvement Lean connaît par ailleurs des développements constants, s’enrichissant de nouveaux outils comme le Lean Startup ou le Lean Management.
Taiichi Ohno restera comme l’un des grands pionniers de l’excellence industrielle au XXe siècle. Il aura non seulement révolutionné l’industrie automobile, mais inspiré de nouvelles façons d’appréhender les processus. Aujourd’hui indissociable de Toyota, le modèle du Lean Manufacturing qu’il a façonné reste une référence guidant les entreprises vers plus de performance, de qualité et de réactivité face aux défis de la compétition mondiale.
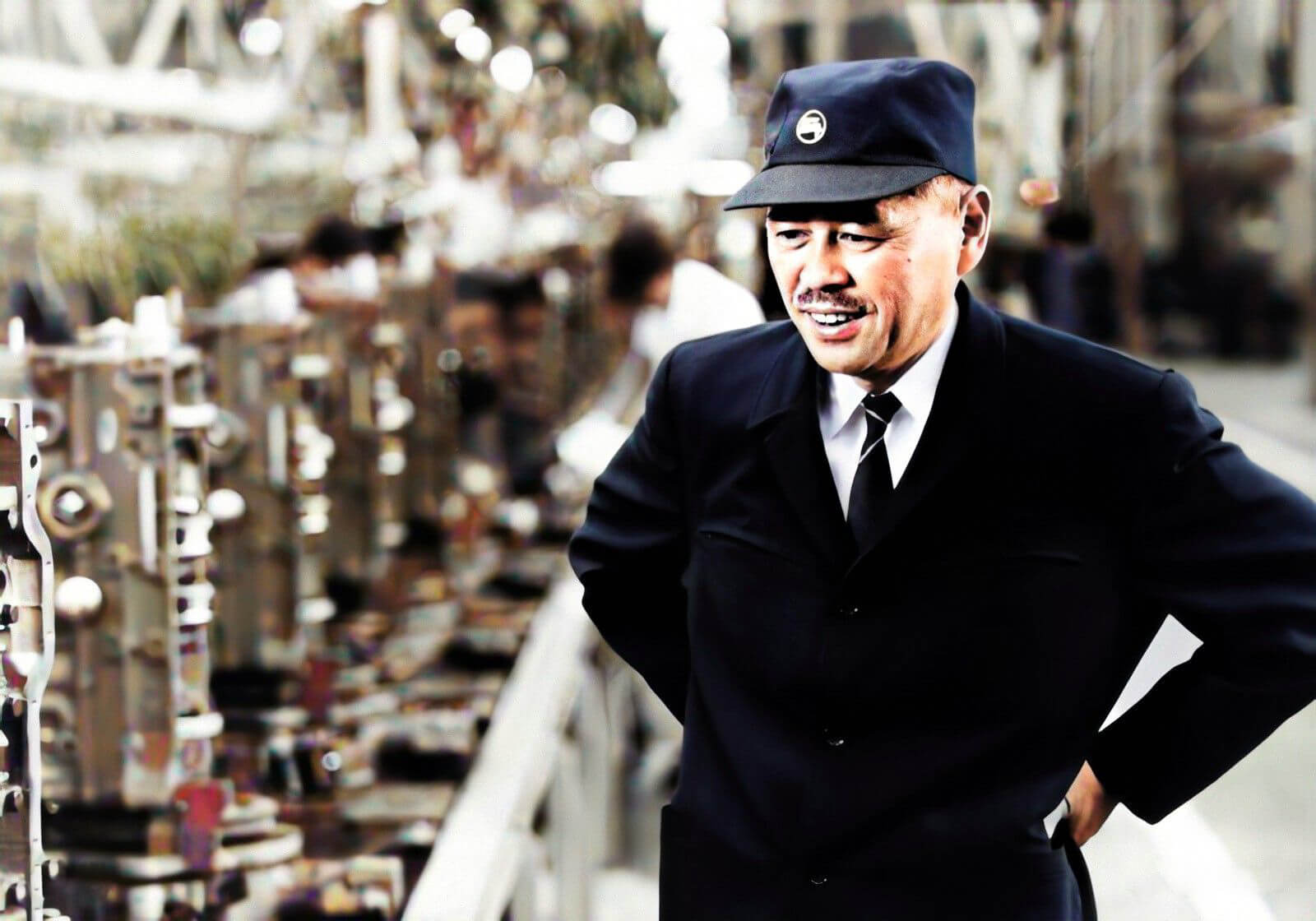