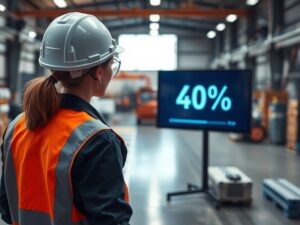
Mesurer le TRS permet aux industriels d’améliorer leurs processus, de suivre les progrès et d’augmenter la productivité des équipements en éliminant les pertes.
Un TRS (Taux de Rendement Synthétique) de 100% représente effectivement une production parfaite, où 100% du temps machine servirait à produire des pièces bonnes. Cependant, il est théoriquement impossible d’atteindre les 100%.
En réalité, un TRS de 85% ou plus est généralement considéré comme excellent dans l’industrie. La moyenne industrielle se situe plutôt autour de 60%. Un TRS inférieur à 60% indique des pertes significatives et nécessite des améliorations.
Pour comprendre pourquoi le TRS n’atteint pas 100%, il est nécessaire de collecter et d’analyser des données sur les causes de sous-performance. Le TRS est calculé en multipliant trois taux : disponibilité, performance et qualité. Chacun de ces facteurs peut impacter le résultat final.
Il est important de noter que dans certains cas, des TRS atteignant ou dépassant 100% ont été rapportés… Ce type d’erreur flagrante nous rappelle que des erreurs moins évidentes sont probablement plus fréquentes dans le calcul et l’interprétation du TRS. Il est donc crucial de mettre en place des processus rigoureux de collecte et de validation des données, ainsi qu’une formation adéquate du personnel impliqué dans le calcul et l’interprétation.
Avant de chercher à améliorer le TRS, il est essentiel de comprendre les six grandes pertes qui affectent le secteur manufacturier. Elles ont été formalisées par Seeichi Nakajima.
1. Pannes d’équipement
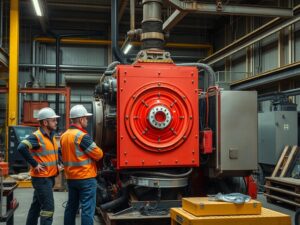
Les pannes d’équipement représentent une cause majeure de perte de disponibilité et de productivité. Ces arrêts non planifiés peuvent avoir un impact significatif sur l’ensemble du processus de production.
Par exemple, dans une ligne d’assemblage automobile, une panne du robot de soudure peut arrêter toute la chaîne, entraînant des retards importants et des coûts élevés. Une étude a montré que les pannes d’équipement peuvent réduire la productivité jusqu’à 20% dans certaines industries.
2. Réglage et ajustement des machines
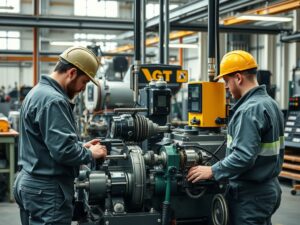
Cette catégorie de pertes concerne le temps d’indisponibilité dû aux réglages, installations ou ajustements nécessaires.
Bien que planifiés, ces arrêts réduisent la disponibilité des équipements.
Dans l’industrie pharmaceutique, par exemple, le changement de production entre différents médicaments nécessite un nettoyage approfondi et un réglage précis des machines, pouvant prendre plusieurs heures. Des techniques comme le SMED (Single-Minute Exchange of Die) peuvent réduire significativement ces temps de réglage.
3. Arrêts mineurs ou micro-arrêts
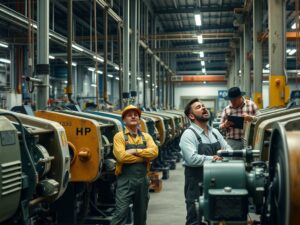
Les micro-arrêts, généralement de courte durée (moins de 5 minutes), sont souvent sous-estimés mais peuvent avoir un impact cumulatif (et donc un coût) important sur la performance.
Dans une usine d’embouteillage, des micro-arrêts fréquents dus à des bouchons mal alignés peuvent réduire la cadence de production de 5 à 10%. L’utilisation de capteurs et d’analyses en temps réel peut aider à identifier et résoudre rapidement ces problèmes.
4. Vitesse réduite
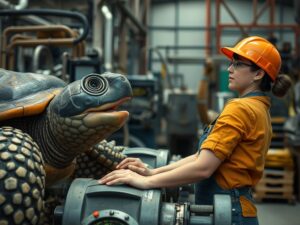
Lorsque la machine fonctionne à une vitesse inférieure à son temps de cycle idéal, elle produit moins que prévu, ce qui constitue une perte de performance.
Dans l’industrie textile, par exemple, des machines de filage fonctionnant à 80% de leur vitesse optimale en raison de vibrations excessives peuvent réduire la production quotidienne de plusieurs centaines de kilogrammes de fil. L’analyse vibratoire et la maintenance prédictive peuvent aider à maintenir les équipements à leur vitesse optimale.
5. Défauts de processus
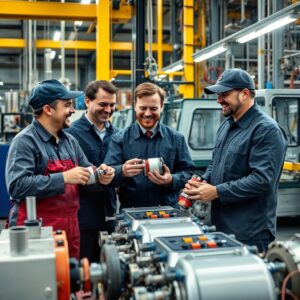
Même lorsque le processus de production semble stable, il peut y avoir des produits défectueux.
Ces produits avec défauts, qu’ils soient réutilisables ou non, sont comptabilisés comme une perte de qualité.
Dans l’industrie électronique, des fluctuations de température dans le processus de soudure peuvent causer des joints défectueux sur les circuits imprimés, entraînant un taux de rejet élevé. L’utilisation de contrôles statistiques de processus (SPC) peut aider à détecter et corriger ces variations avant qu’elles ne causent des défauts.
6. Moindre rendement ou taux de rebut élevé
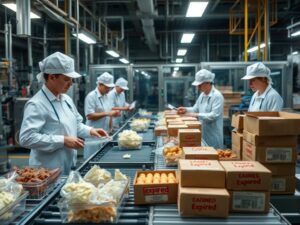
Cette perte se produit souvent après des changements de production, où le rendement est réduit en raison de défauts de processus.
Par exemple, une mauvaise configuration lors d’un changement de série peut entraîner un nombre important de produits rejetés au démarrage, ce qui affecte le TRS. Les techniques de types SMED ou Poka Yoke sont cruciales.
Au delà de tous ces outils de mesure, les pertes sont parfois diffuses, et il ne faut pas négliger les visites sur le terrain et pratiquer un Gemba Walk. Il ne s’agit pas d’une inspection ou d’un audit, mais de mettre en place une démarche collaborative et proactive visant à renforcer la communication.
Références
- Muchiri, P., & Pintelon, L. (2008). Performance measurement using overall equipment effectiveness (OEE): literature review and practical application discussion. International Journal of Production Research, 46(13), 3517-3535.
- Nakajima, S. (1988). Introduction to TPM: Total Productive Maintenance. Productivity Press, Cambridge, MA.
- Jonsson, P., & Lesshammar, M. (1999). Evaluation and improvement of manufacturing performance measurement systems – the role of OEE. International Journal of Operations & Production Management, 19(1), 55-78.